 |
MODULE 7: SOCIOLOGY OF WORK, INDUSTRIAL RELATIONS AND LAW SECTION 1: THE CAPITALIST LABOUR PROCESS: Neo-Fordism in the Western Cape |
NEO-FORDISM IN THE WESTERN CAPE:
Ewert studied four firms in the Western Cape, embracing
- engineering
- can manufacture
- electronics
- clothing
They had more or less the following in common:
- They were striving striving to become more competitive or to survive.
- They introduced micro-electronic technology.
- Three of the four have information systems to check on waste and rework costs.
- Two of these restructured their factory lay-out towards manufacturing cells.
- Three improved quality.
- There was a modest progress in reducing lead times and work-in-progress.
- Downtimes and changeover times are still lengthy.
- They developed a more co-operative approach towards labour. Worker participation was seen as necessary.
- They introduced "green areas" used as briefing and discussion forums.
Engineering Firm:
This firm is a manufacturer of diesel engines, .started in 1980 for strategic reasons. Its output target was 55 000 engines per year. However, the maximum ever achieved 23 000 per year.
The situation changed in 1990 with cessation of hostilities in Angola, when the firm was forced to sink or swim. The battle for survival forced "downsizing" and flexibility:
- the target production was reduced to10 000 engines per year;
- the management was reduced from 43 to 16;
- the workforce was cut from 6 000 to 2 500;
- workers became multi-skilled: each operator has a working knowledge of 30 machines (lines consist of 20 to 47 machines);
- flexibility was built into many computerised numerical control machines and a flexible specialisation centre.
- the changeover times was reduced from 28 to 6 shifts;
- the firm concentrated on the manufacture of high quality engine blocks, crank-shafts and camshafts.
- the firm breaks even (covers costs) at 20% of manufacturing capacity.
However, the dependence on overseas suppliers means no just-in-time production, and consequently, they have
- an inventory of 50 000 parts;
- lead times still up to 8 months.
The firm experiences relatively stable industrial relations system after a strike by NUMSA members in the late 1980's. This can be ascribed to a more participative approach:
- quality circles;
- extensive communication system;
- shop stewards council;
- restructured company's grades from 9 to 5 levels.
Can Manufacturer:
This is a.firm that dominates the South African can manufacturing market. The impetus for change came after take-over by Nampak in 1988. A survey showed that:
- the technology was outdated: machines were 25 to 30 years old;
- output produced irrespective of quality;
- the workers felt that they could contribute to running of the plants, but that were not given the opportunity.
Bearing this in mind,the firm committed itself to quality production and a participative management style with Japanese methods. They
- retrenched some middle managers with old bureaucratic English style;
- introduced "green areas" to discuss production targets and problems;
- intoduced multi-skilling training: "down line" rather than "across line" specialisation;
- flattened job hierarchy.
Co-operation and participation of workers was regarded as the biggest success by management. This was ascribed to absence of union and recruitment from families of workers.
The results were:
- productivity rose by 20%;
- a reduction in the cost of rework from R8.9 to R5.6 million;
- increased profits (wages were not part of the study).
Electronics Firm:
A pilot project was initiated, resulting in the introduction of a telecommunications cell team for cellular manufacture. This reduced lead time and work-in-progress by 50%.
Manufacturing cells were introduced into whole of Telecommunications area (telecommunications). Total involvement process was advocated by industrial engineer. There was a switch from "western style management" where bosses do the thinking to "Japanese style" where management mobilises the intellectual resources of all employees.
Clothing Firm:
This firm operates 13 factories, employing 2000 people. They manufacture expensive ladies' summer wear. It is a leading firm, with considerable export success, with a European market in high quality garments an having a world class design ability. They adopted:
- a just-in-time approach.
- the front end sections are thoroughly computerised: the characteristics of every roll of textile fabric is fed into computer's information system; the styles, sizes, colour, and so forth are "marked in" and computerised equipment cuts patterns with enormous speed, accuracy and minimum waste.
- the back sections are solidly based on Taylorist principles: machine room divided into 25-30 machinists with one supervisor, one quality controller and one work study officer; after measuring the time spent on each operation by stopwatch, the standard rates of payment are set; operators' productivity is measured every two hours.
- the inventory was reduced from 20-25 days' stock to 10 days.
- just-in-time production is more demanding on managers and operators: there is less room for error, workers have to be quick thinking.
A good relationship between employers and trade union is considered important. The relationship with SACTWU described as "constructive conflict".
Conclusion:
- All four firms developed a marketing and manufacturing strategy to become more competitive or simply to survive.
- This involved installing powerful information systems (3 out of 4), and restructuring factory layout and work organisation (2 out of 4).
- There was a shift to neo-Fordism, not post-Fordism (flexible specialisation).

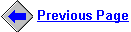