 |
MODULE: INTRODUCTION TO ERGONOMICS |
THE PROCESS OF ERGONOMIC WORKPLACE RISK ASSESSMENT:
STEP 1: Identify the hazards - Review existing records
- Review records of musculoskeletal injuries, including repetitive trauma disorders, along with information about the related task or activity and probable causes.
- Worker complaints of discomfort.
- High absenteeism, frequent clinic visits.
- Identify and analyze trends or problems related to particular departments, areas, job functions, workstations, etc.
- Check the job descriptions: for those jobs requiring repetition and exertion, frequent heavy lifting or overhead lifting/work or use of vibration equipment.
The outcome of the initial assessment should be an identification of tasks, operations and processes needing improvement, modification or other controls to eliminate or minimize ergonomic hazards, increase comfort and optimize performance.
STEP 2: Setting up the infrastructures
- Ergonomic programmes should be regarded as part of the general safety programme and should be integrated into the company’s current occupational safety and health activities.
- Management commitment: management must issue a policy statement, appoint responsible personnel to champion the programme, give ergonomic improvements equal priority with cost reduction, productivity and quality assurance activities, encourage employee involvement and commit resources for: training, consultants and implementation of ergonomic improvements.
- Benefits of worker involvement include increased motivation/job satisfaction, added problem-solving capabilities and greater acceptance of change.
- Hazard identification, task analyses and the development and implementation of control measures require input from safety managers, health care providers, human resources personnel, engineering personnel, purchasing personnel and ergonomics specialists.
STEP 3: Training.
Training of employees is critical to the success of an ergonomics program. Both employees and managers require the knowledge to recognize potential risk factors for injuries and their prevention. The more aware the workers are of musculoskeletal hazards in their workplace the more likely they are to work towards reducing injuries. Training employees ensures that they are informed about the hazards in their work place so that they can actively participate in identifying and controlling exposures. Training programmes should be directed according to the needs of the employer/employee and should include programmes for managers, supervisors, job specific training, engineer personnel and general awareness training.
Ergonomic awareness training should consist of the following:
- Identify the signs and symptoms of WMSDs and the importance of early reporting.
- Recognize workplace risk factors for WMSDs and understand general methods for controlling them.
- Recognise the employee’s role in the process, employees know their jobs better than anyone else knows and are often the source of ideas to improve them.
- There should be open interaction between trainer and trainees.
- Employees need to know the procedure for reporting ergonomic risk factors and musculoskeletal disorders.

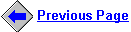
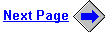

General Introduction to
Occupational Health: Occupational Hygiene,
Epidemiology & Biostatistics by Prof Jonny
Myers is licensed under a Creative
Commons Attribution-Noncommercial-Share Alike
2.5 South Africa License.